Application of 20-year System Warranty PVC Roofing System in Apple Data Center Project
Abstract:Taking the roof of a APPLE Data Center in Guizhou as an example, the article introduces application of 20-year system warranty PVC roofing system on data center roofs. Due to the complex structure and importance of the roof waterproofing, the paper analyzes the main structure and application advantage of PVC roofing system, and gives a brief introduction of the main construction technology of and roof details.
Key words:Data center; single layer roofing system; PVC waterproofing membrane; 20 year system warranty
1. Project Background
The Apple Guizhou Data Center is located in the Guizhou Province, Guian New District. The overall investment scale of the project is 1 billion USD, and construction began at the end of 2018, with a total building area of nearly 50,000 square meters, divided into three main functional areas: data center, generator room, and equipment area, designed and constructed strictly according to LEED Gold certification requirements.
The project requires compliance with American design practices and provides a 20-year overall warranty for the roofing system. After selection and strict examination by the owner, design party, management company, and general contractor, it was finally decided to use the Sika PVC roofing waterproofing system for the steel structure roofs of the data center and generator room, with the roofing waterproofing project covering more than 50,000 square meters, constructed by Beijing Guzhuo Construction Engineering Co., Ltd.
2. System Design and Material Selection
2.1 Roof Structure Layers
The roofing construction method of this project follows the American data center system design standards, meets the domestic first-level waterproofing requirements, and selects roofing system materials according to the 20-year system warranty requirements. The waterproof layer uses 2.0mm thick Sika fiberglass reinforced backing non-woven PVC waterproof membrane, fully adhered to the fiber gypsum board, and fixed with Sika fasteners to the base steel plate. The insulation layer uses Rockwool insulation board (120mm thick for the data building, 140mm thick for the generator building, double-layered). The vapor barrier layer uses 1.0mm thick TECHNONICO SBS self-adhesive membrane, adhered to the fiber gypsum board base.
The overlapping parts of the Sika PVC membrane are welded with hot air, and the strength of the welds is completely consistent with the performance of the base material. The roof details use specialized PVC membranes for construction, and customized PVC prefabricated parts are used for drainage outlets and pipe penetrations, creating an overall waterproof effect for the roof.
The wind load calculation for the roof needs to consider both the bonding strength of the membrane and the layout of the fasteners for the fiber gypsum board. According to FM roofing system certification, the same fully adhered Sika PVC membrane system can withstand wind loads of up to 255 psf, far exceeding project requirements. The layout of the fasteners for the gypsum board is calculated based on project design requirements, referencing FM system combinations that meet the requirements.
The main layers of the roof are as follows:
1) 2.0mm Sarnafil G410-20LF PVC waterproof membrane
2) Sika Sarnacol-2170 contact adhesive
3) 12.7mm thick DensDeck roofing fiber gypsum board, mechanically fixed
4) Data building 120mm (2X60 staggered overlap) Rockwool insulation board, density 180kg/m³
Generator building 140mm (2X70 staggered overlap) Rockwool insulation board, density 180kg/m³
5) 1mm TECHNONICO self-adhesive modified bitumen waterproof vapor barrier membrane
6) 12.7mm thick DensDeck-Roof Board roofing fiber gypsum board
7) 1.0mm thick profiled steel plate, (YX38-152-914) mechanically fixed
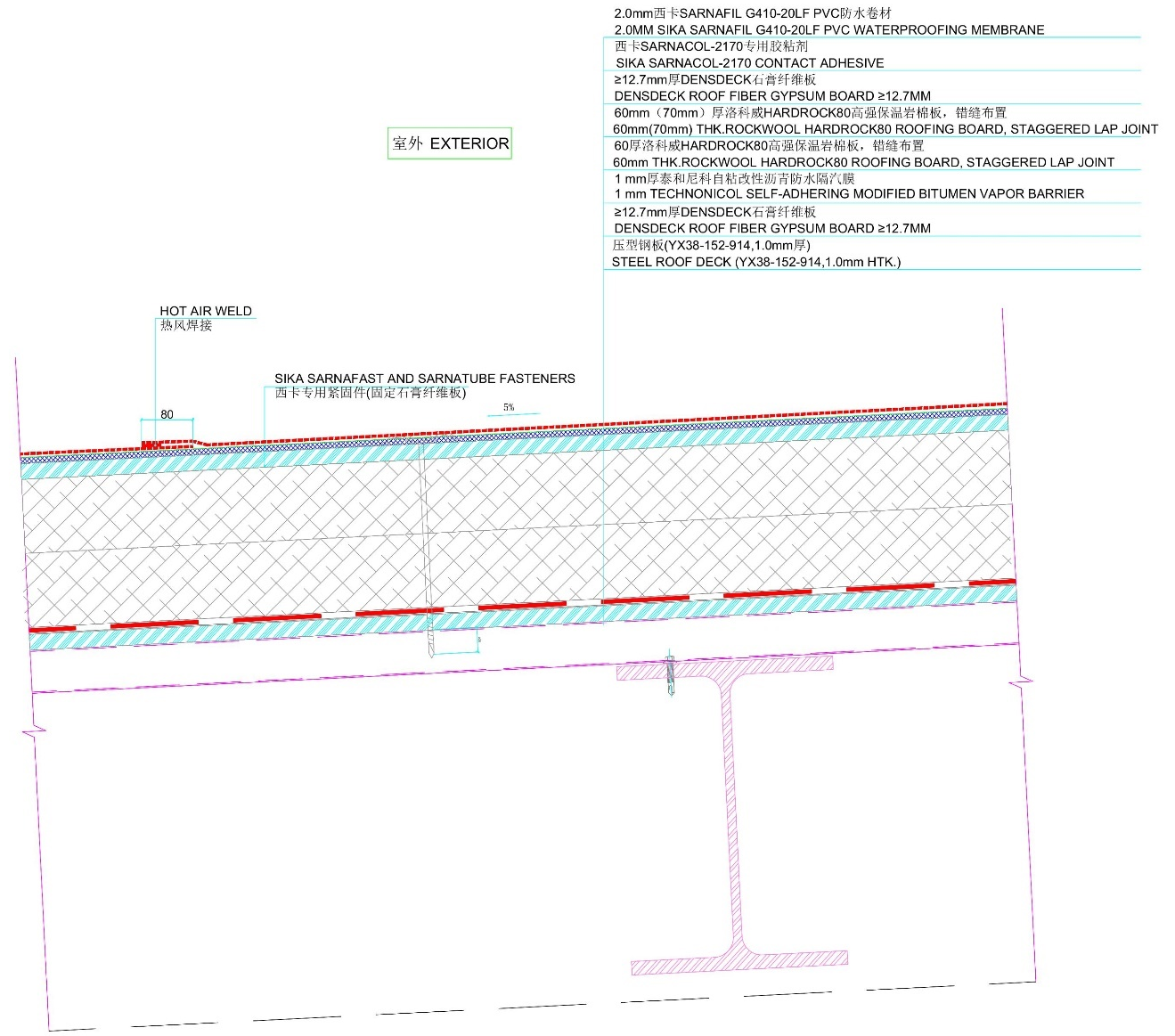
2.2 System Advantages
1) Sika PVC waterproof membrane has excellent performance, produced using imported raw materials, certified for a lifespan of up to 35 years by BBA. The white surface and self-cleaning function give the membrane a high solar reflectance and energy-saving effect, meeting LEED certification requirements. It has excellent low-temperature flexibility at -40℃, and the fiberglass reinforcement provides outstanding dimensional stability and good mechanical impact resistance.
2) The DensDeck roofing fiber gypsum board used in the project is imported from the United States, with enhanced fiberglass facing on both the front and back, providing a good bonding base for the waterproof and vapor barrier layers, with a gypsum core. Its excellent performance compared to paper-faced gypsum board and magnesium oxide board can more effectively protect the waterproof base from issues such as sand, bulging, delamination, and deterioration, as well as damage during construction.
3) The insulation layer uses Rockwool insulation board, which has FM certification and is certified for "non-combustible core material" (NCC), with a water repellency rate of over 99.5%, long-term water absorption rate ≤1.5KG/M2, and excellent long-term thermal insulation performance.
4) The vapor barrier layer uses 1.0mm thick TECHNONICO SBS self-adhesive vapor barrier membrane adhered to the gypsum board base, forming a sealed layer with good waterproofing effect. This vapor barrier layer has self-healing properties, providing excellent encapsulation at the points where screws penetrate the base steel plate.
5) The fasteners and adhesives used in this project are all provided by Sika, and the system's safety and durability have undergone multiple rigorous tests and verification from over 30 years of application in foreign projects.
3. Analysis of Key Construction Difficulties in the Roofing System
3.1 Project Implementation Challenges
1) The uninterrupted massive data exchange volume of the data center requires a stable and reliable physical environment, maintaining a constant temperature and humidity. The valuable equipment in the data center also imposes extremely stringent requirements on the roof waterproofing system, and the 20-year system warranty places very high demands on construction control and detail handling.
2) The roof system and detailed node practices of this project are in accordance with the construction standards for data centers in the United States. Many roof detail node practices are being designed for the first time in the country, and some node practices need to be confirmed through multiple discussions among Sika, contractors, general contractors, management companies, and designers, making the construction difficulty very high.
3) Guizhou has a subtropical plateau monsoon humid climate, with highly variable weather. The tight construction schedule imposes extremely high requirements on the protection and control of the construction process, requiring overcoming many factors such as adverse weather affecting adhesive construction.
4) The roof of the data center has a large span and a large water collection area. Since the roof uses an external drainage method, it is necessary to use special compressive rock wool strips to find the slope in the transverse direction of the parapet wall to ensure that the roof will not accumulate water.
5) The roof structure has multiple layers, a variety of auxiliary materials and accessories, and multiple subsystems: it includes seven layers of materials above the structural layer, with more than 10 types and lengths of fasteners. There are also subsystems such as lightning protection systems, pedestrian maintenance paths, lighting systems, and drainage systems on the roof.
6) Various materials for the roof are imported from multiple countries including the United States, Germany, Switzerland, and Russia, with nearly 60 containers of various imported materials and over 100 vehicles for domestic transportation. During peak periods, nearly 70 personnel are on site, posing a great challenge to the organization of construction and progress management on site.
3.2 Construction Process
Acceptance and delivery of the roof base layer→Roof cleaning→Construction of the first layer of DensDeck gypsum board→Construction of self-adhesive vapor barrier layer→Construction of rock wool insulation board→Construction of the second layer of DensDeck gypsum board→Construction of PVC waterproof membrane bonding→Processing of nodes such as corners, parapet walls, equipment bases, and rainwater outlets→Completion cleaning→Water spray test→Finished product protection→Completion acceptance
3.3 Important Construction Links and Highlights
(1) Adhesive bonding effect testing
This imported Sika professional adhesive is being used in the country for the first time. Testing needs to be conducted for different construction methods, adhesive amounts, and environmental impact factors to meet bonding strength while also considering the best solution for construction efficiency.
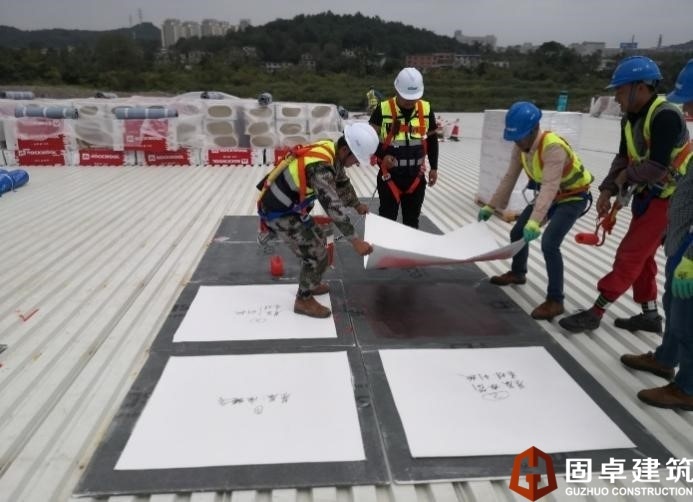
(2) Welding tests before membrane construction
Large area welding uses the Swiss Leister automatic welding machine. To ensure the welding effect of the membrane, daily welding effect tests are required, adjusting the temperature and speed of the welding machine according to the variable local climate conditions in Guizhou.
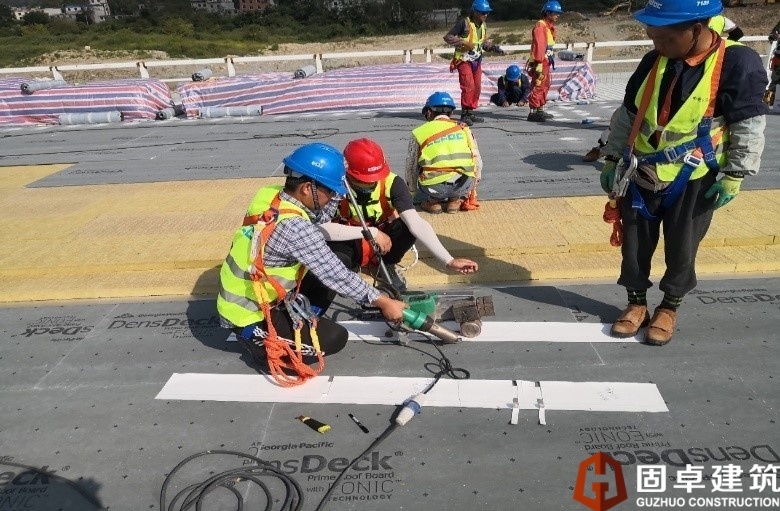
(3) Base layer cleaning before membrane bonding
The fixing construction of the gypsum board generates a large amount of gypsum powder, posing a risk to the bonding strength of the membrane. The project uses a large vacuum cleaner to clean the base layer, greatly improving efficiency and cleanliness.
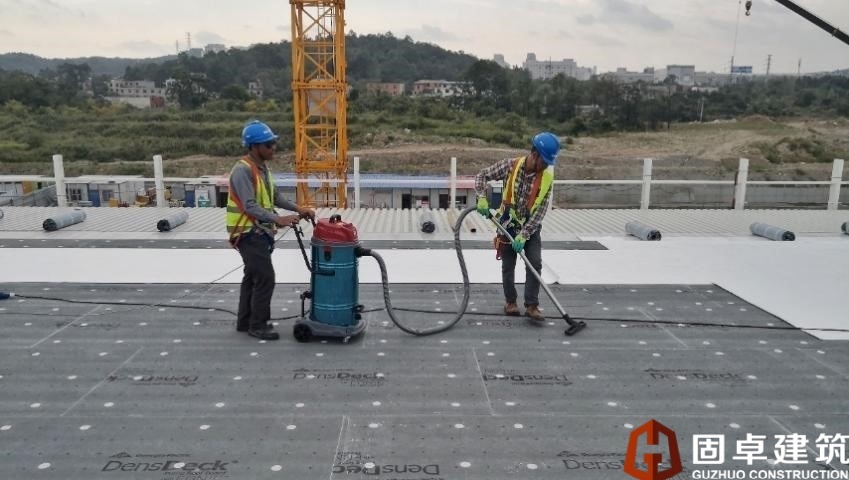
(4) PVC membrane bonding construction
The adhesive is applied in two coats. The first coat is a thin layer to seal the base layer, and after the first coat dries, the second coat of adhesive is applied while simultaneously brushing and laying the PVC membrane. To ensure bonding effectiveness and prevent issues like bubbling, a weighted roller is used for multiple compressions based on on-site experience.
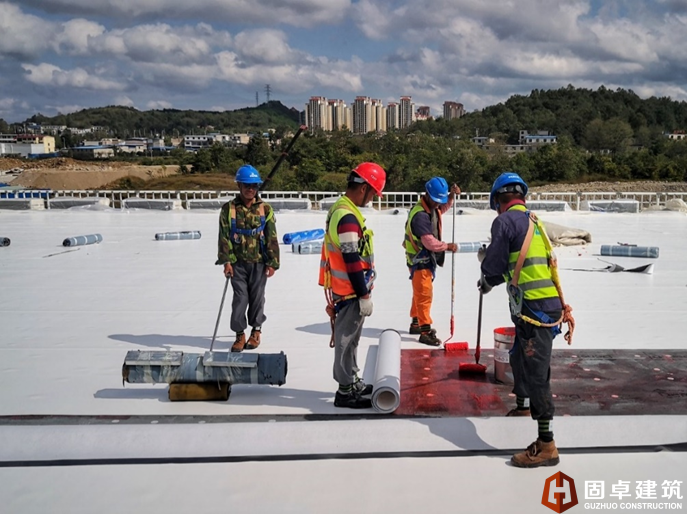
(5) PVC membrane welding
All long and short edges of the large area membrane are welded using an automatic welding machine to reduce human error. For nodes such as parapet walls and gable walls where automatic welding cannot be used, workers are required to perform two manual welding operations with a handheld welding gun to ensure the long-term effectiveness of the welding.
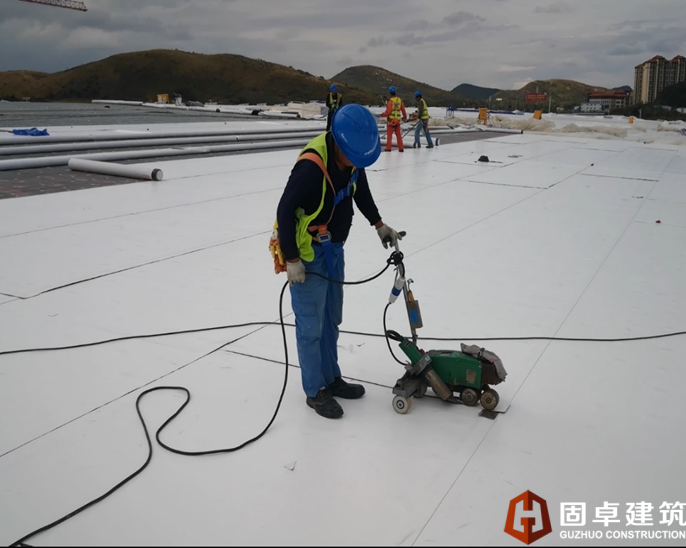
4 Main Detailed Node Design and Processing
4.1 Parapet Waterproof Node
The large area membrane is disconnected at the bottom of the parapet wall and fixed with U-shaped pressure strips. The vertical PVC membrane is bonded to the gypsum board using professional adhesive to prevent wind pressure effects, and then the edge is finished with a closure strip to the outside of the parapet wall, treated with weather-resistant sealant. The bottom of the parapet wall is welded to the large area PVC membrane using a hot air welding machine.
Slope design scheme: The roof has no gutters. To reduce water accumulation, special compressive rock wool strips are used on site to find the slope between the rainwater outlets, cut by the Rockwool factory. The slope is found in different steps of 4CM, 3CM, 2CM, and 1CM between the two rainwater outlets to minimize the impact on the upper gypsum board and membrane laying.
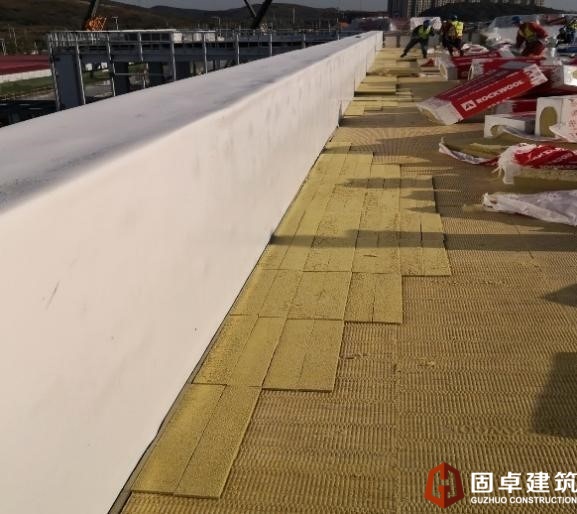
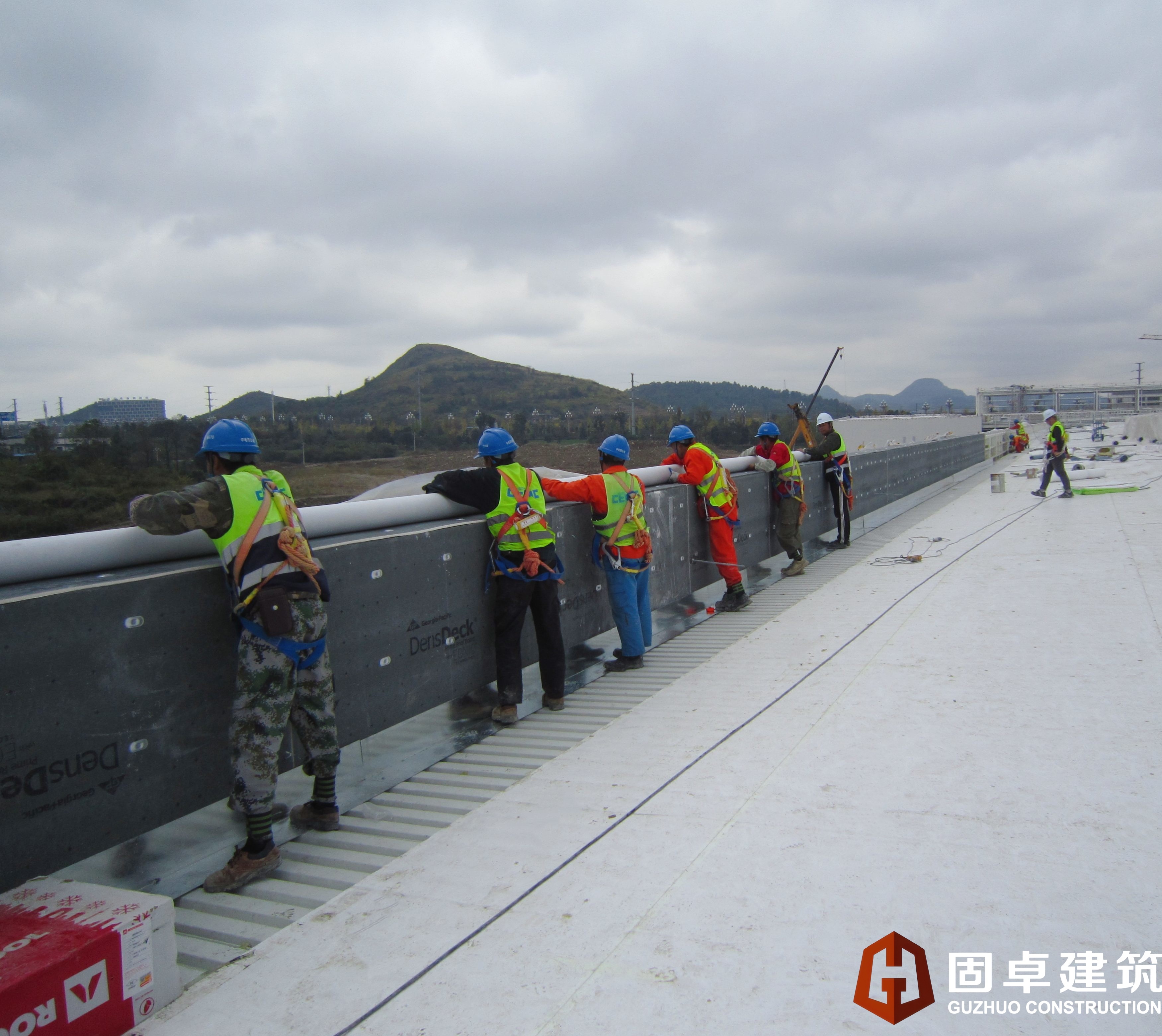
4.2 Drainage and Overflow Node
The roof uses an external drainage method to guide rainwater through the drainage outlet to the outside of the parapet wall rainwater outlet, and an overflow outlet is also set up. There are as many as 153 rainwater outlets on the roof. The complex node of the rainwater outlet is difficult to handle, so prefabricated rainwater outlet components designed in cooperation with Youer Metal are used, which can be directly welded to the large area membrane after installation, avoiding the possibility of leakage from the rainwater outlet.
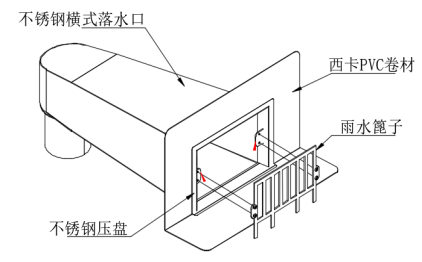
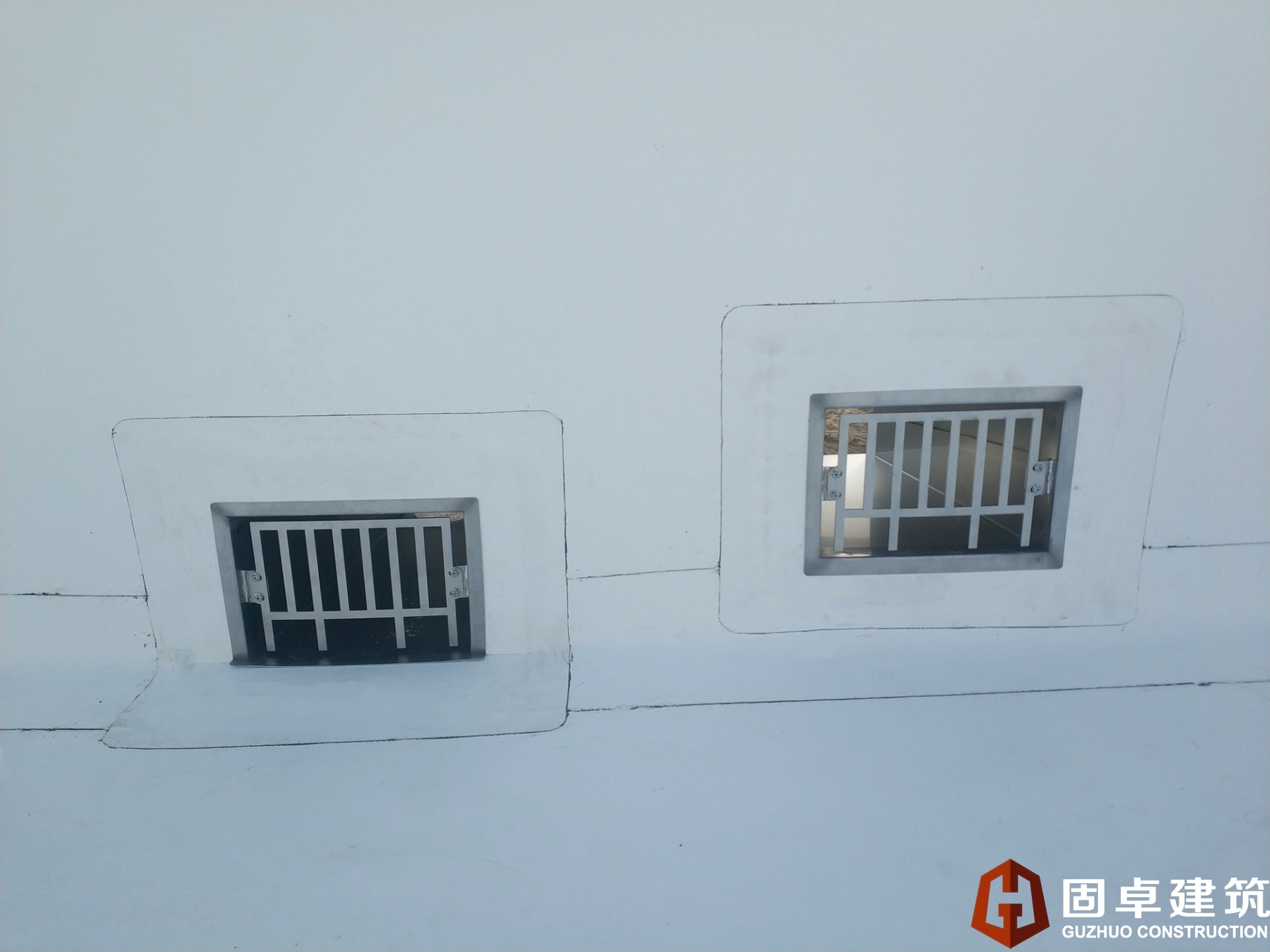
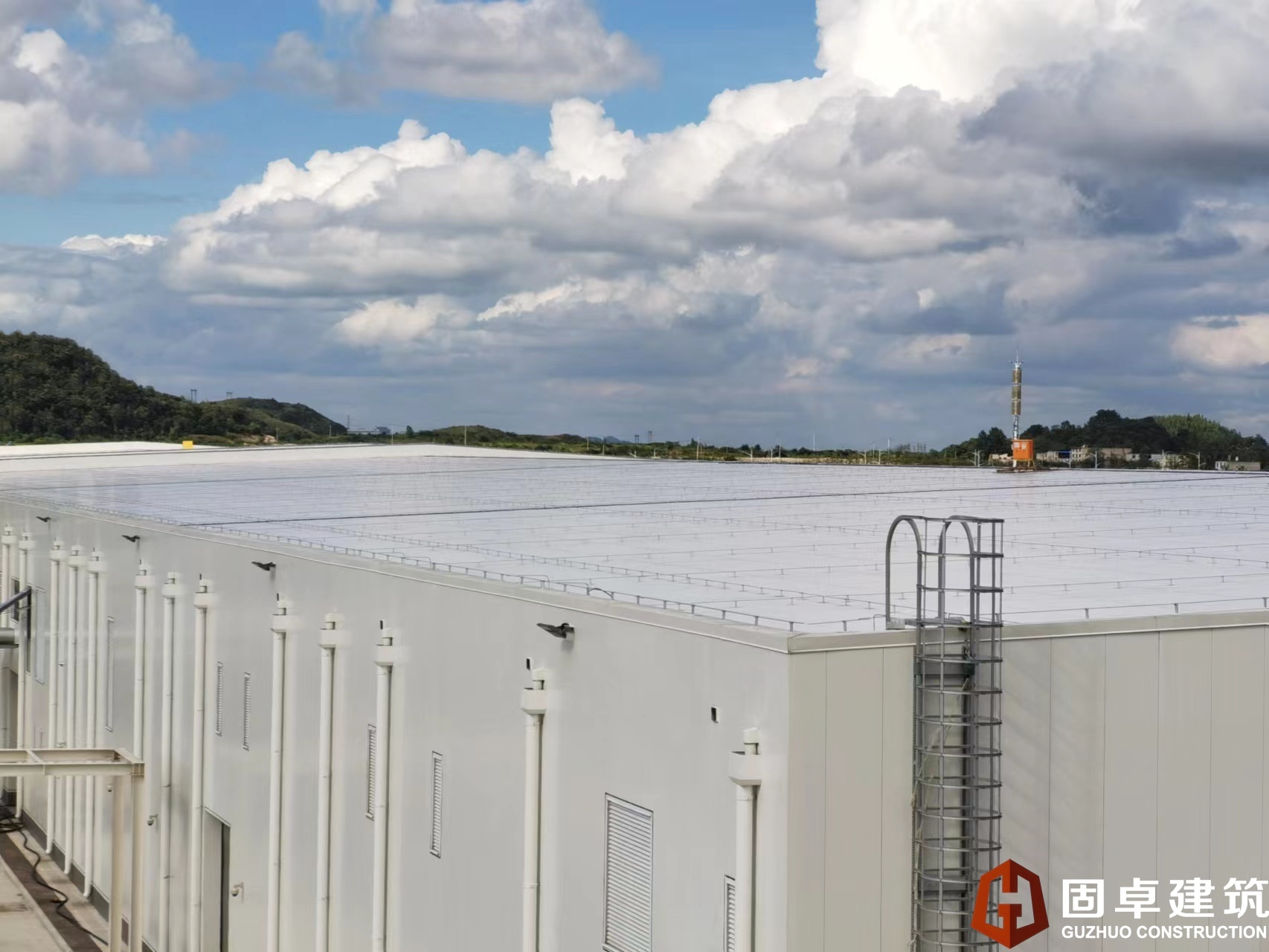
4.3 Silencer Platform Waterproof Node
To isolate the noise from the indoor generator set, 32 louvered windows on the low cross roof are equipped with silencer platforms. The complex structure of the silencer makes waterproofing particularly difficult. After extensive discussions, it was finally decided to install channel steel on the platform, with the PVC membrane edge at the top of the channel steel, and water holes set up to facilitate the smooth drainage of rainwater. The drainage outlet is also installed using prefabricated rainwater outlet components.
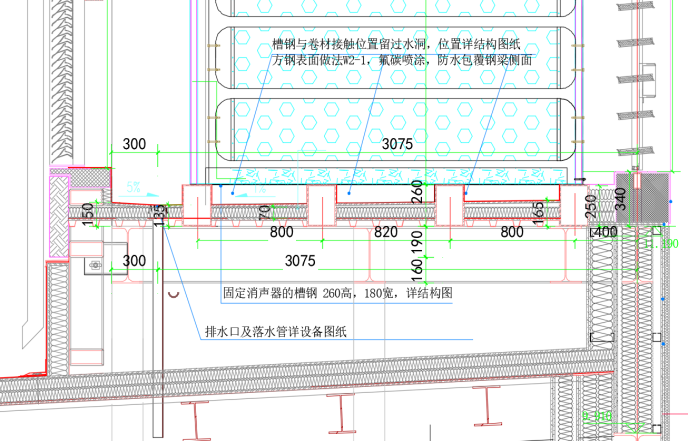
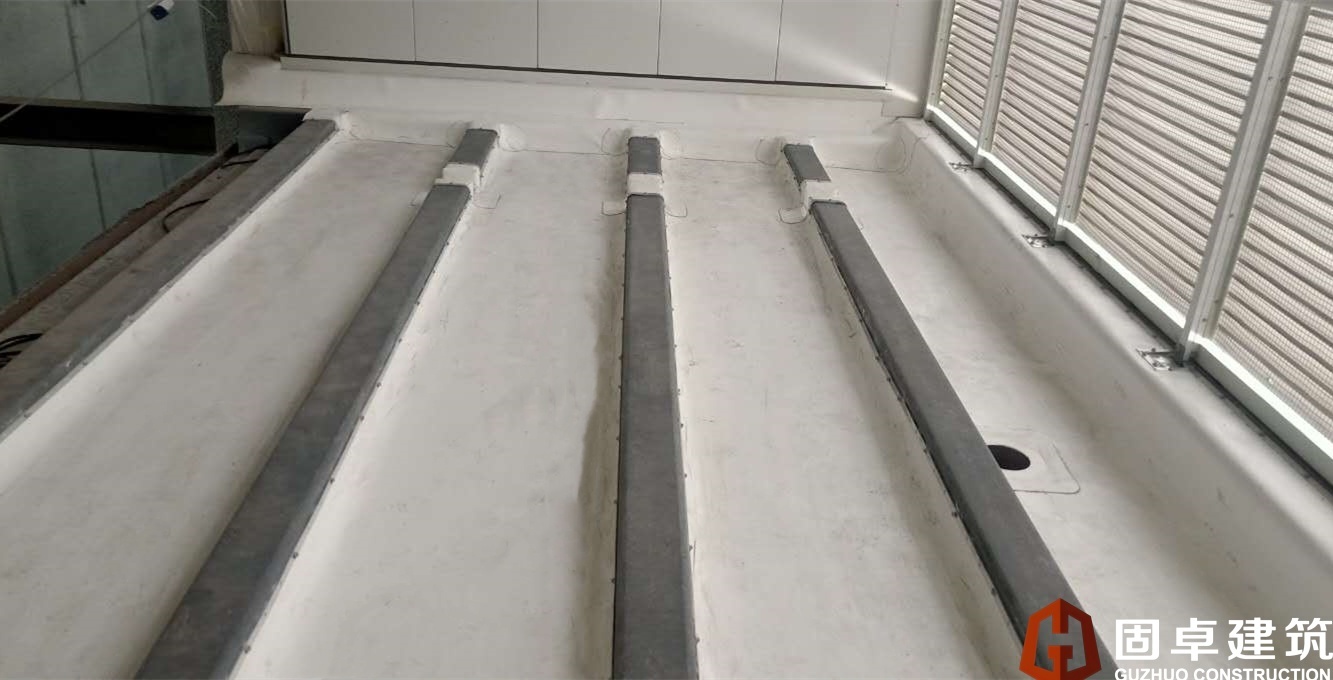
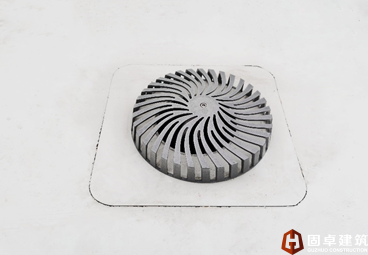
4.4 Roof Maintenance Path, Lighting Pipeline, and Lightning Protection System
To ensure the integrity and aesthetics of the roof system, the maintenance path, lighting pipeline, and lightning protection system on the roof all use single-layer roof-specific auxiliary material accessories. The maintenance path is paved and welded with PVC walkway boards produced by Sika, and the lighting pipeline and lightning protection system are provided by prefabricated PVC components from Youer Metal.
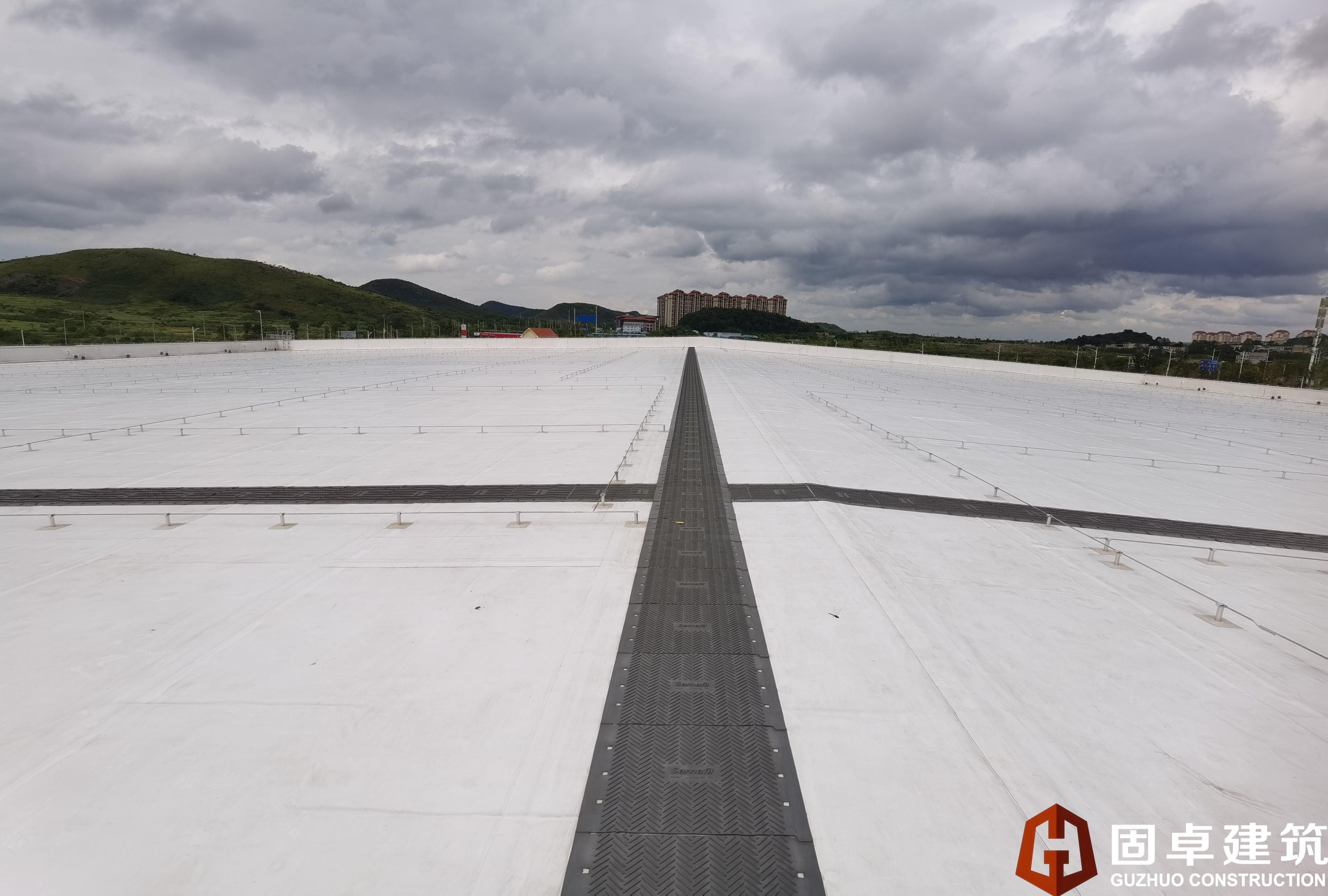
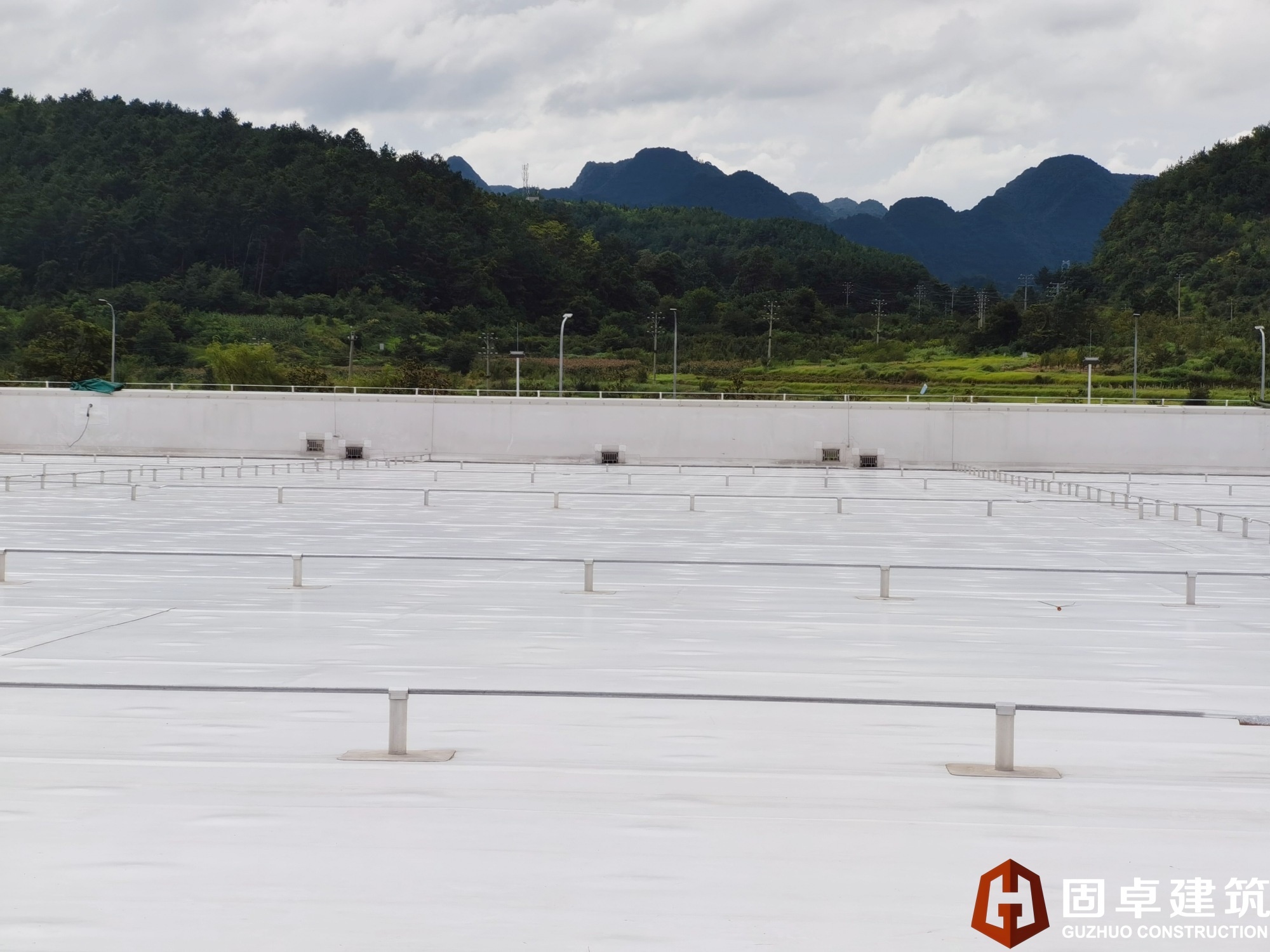
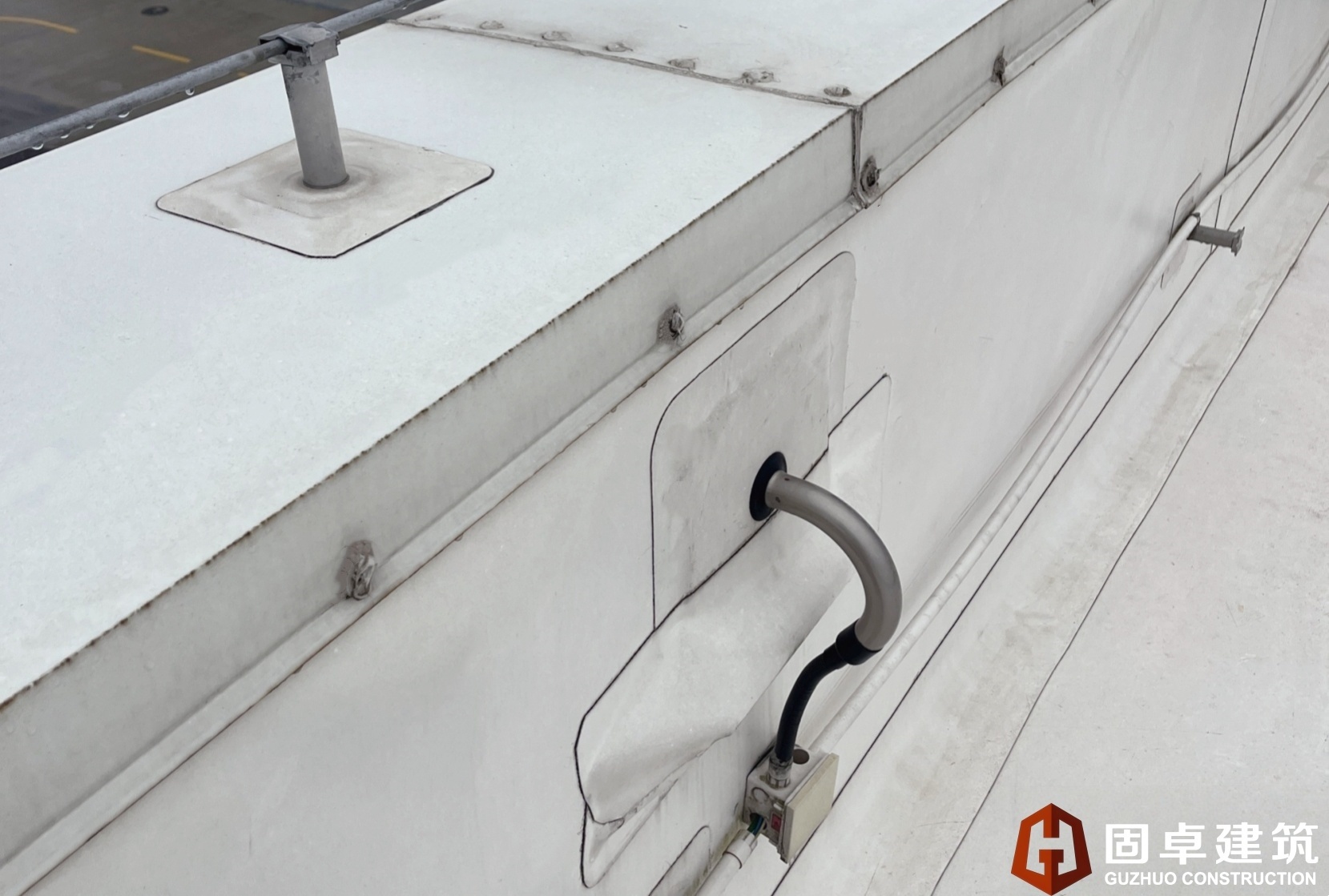
5. The roofing contractor specializes in design, construction organization, and close cooperation with Sika.
The owner has very strict requirements for the selection of roofing products, auxiliary materials, node design, and construction plans. Beijing Guzhuo Company, after multiple discussions with Sika, designers, and the general contractor, submitted the plan for revisions several times before finally obtaining approval from the owner's headquarters. The construction process and results of the project have also received unanimous recognition from all parties in the project department.
Sika provides a 20-year overall quality guarantee for the roofing system, imposing strict requirements on the construction of the roof. Sika arranges technical service engineers to supervise and guide the site throughout the process, and regularly prepares reports to report to Sika's headquarters. Sika's Swiss headquarters also arranges technical experts for multiple guidance inspections to ensure that the roofing system is constructed according to Sika's international quality standards, with Sika and Guzhuo working closely together to create a high-quality roofing project.
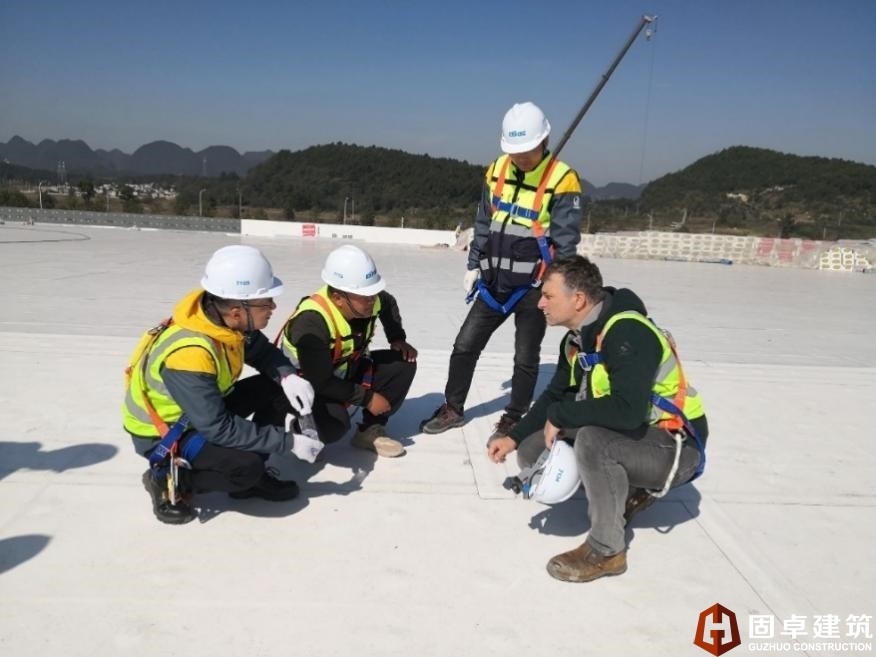
6. Project Significance
This data center is built strictly according to LEED green building certification requirements, and Sika's high-quality single-layer roofing system provides very beneficial reference value for domestic data center construction.
This project is the first in Sika China to provide a 20-year roofing system warranty. All auxiliary materials and accessories used in the roofing system are provided by Sika and constructed strictly according to Sika's quality standards, serving as a good model for the promotion and practice of the 20-year roofing system warranty in the future. After nearly five years of use, the surface of the membrane remains as clean and bright as new, and there have been no leakage issues with the roof, ensuring the safe operation of the database due to excellent construction quality.
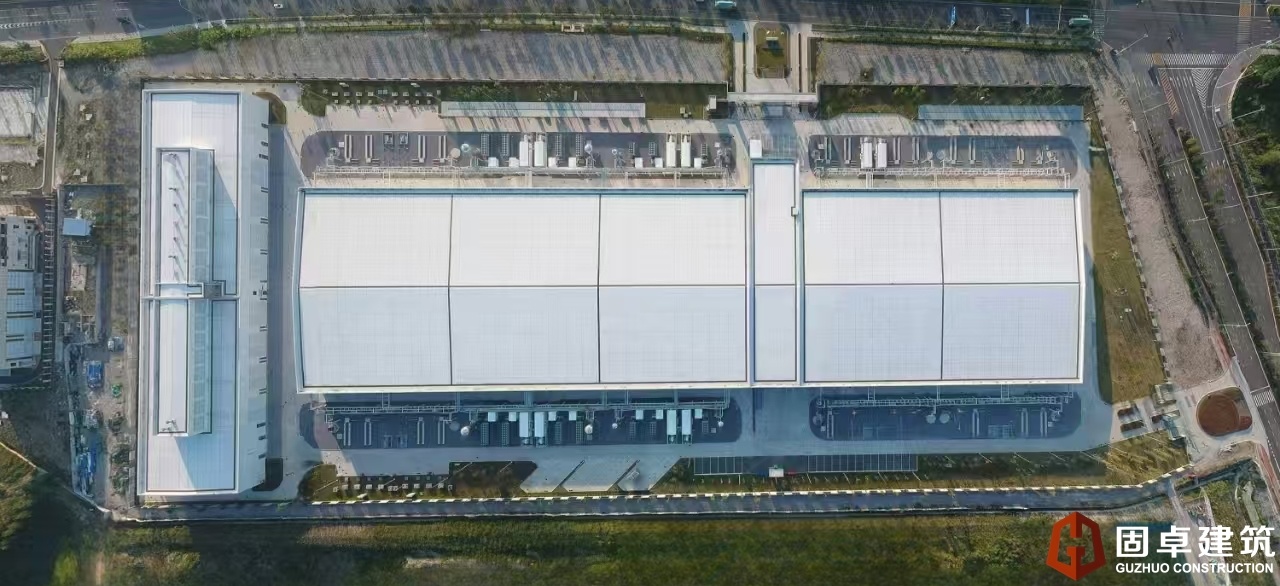
Aerial photos of the completed roof
Beijing Guzhuo Construction Engineering Co., Ltd. also undertook the anti-corrosion engineering for important areas of this project, including the fire water tank, oil tank area, diesel pipe trench, transformer oil discharge tank, outdoor ramps, and steps.
Related news